Ultrasonics
Ultrasonic Waves Characteristics and Velocity
Ultrasonic waves are high frequency sound waves with a frequency higher than 20 kHz. They are used in a variety of industrial and medical applications. The characteristics of ultrasonic waves include high frequency, high amplitude, and the ability to travel through various materials. The velocity of ultrasonic waves is dependent on the properties of the medium it is traveling through.
Velocity of ultrasonic wave through a solid material,
$$ v =\sqrt{\frac{Y}{\rho}} $$ where Y is youngs modulus of material and \( \rho \) is the density.Velocity of ultrasonic wave through a liquid,
$$ v =\sqrt{\frac{K}{\rho}} $$ where K is bulk modulus of liquid and \( \rho \) is the density.Velocity of ultrasonic wave through a gaseous medium,
$$ v =\sqrt{\frac{\gamma P}{\rho}} $$ where P is pressure of gas and \( \rho \) is the density.Production of Ultrasonic Waves
The principle behind generating ultrasonic waves is to make a dense material vibrate rapidly, causing the air around it to vibrate at the same frequency and spread out as ultrasonic waves. Ultrasonic waves can be produced through various methods, including magnetostriction oscillators and piezoelectric oscillators.
Magnetostriction effect
Magnetostriction is a property of ferromagnetic materials which causes them to expand or contract in response to a magnetic field. If we can provide direction changing magnetic field to a ferromagnetic rod, it will expand and contract continously as in a vibration. This type of vibration with higher frequency can be produced with help of an electrical oscillator like LC circuit.
Magnetostriction Oscillator
A magnetostriction oscillator is a device that uses the magnetostriction effect to generate ultrasonic waves. It consists of a ferromagnetic rod, typically made of nickel-iron alloy, that is placed in a magnetic field. When an alternating current is applied to the rod, it changes shape due to the magnetostriction effect, and this continous vibration ( expansion & contraction of rod) generates ultrasonic waves.
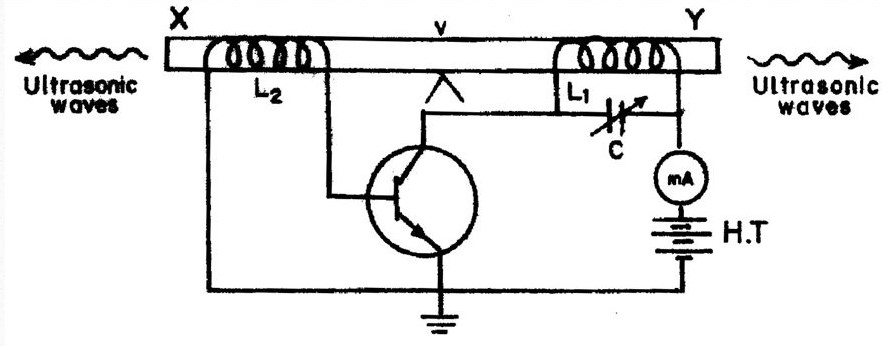
Construction
- The ferromagnetic rod have coils L1 and L2 wound around their ends.
- The coil L1 is connected to the collector of a transistor.
- The coil L2 is connected to the base of the transistor.
- The frequency of the oscillatory circuit (LC) can be adjusted by adjusting the capacitor C.
- The current can be measured by a milliammeter connected across the coil L.
- The battery connected between the emitter and collector provides necessary biasing for the NPN transistor.
Working
When a ferromagnetic rod is placed inside a magnetic coil that carries an alternating current, the rod experiences a change in length for each half cycle of the current. This means that the rod vibrates with a frequency that is twice that of the frequency of the alternating current. The amplitude of these vibrations is usually small, but if the frequency of the alternating current matches the natural frequency of the rod, the amplitude of vibration increases significantly due to resonance.
- When the battery is turned on, the transistor produces current.
- This current will produce electrical oscillations in LC circuit or tank circuit.
- This current is then passed through the coil L1, which causes a corresponding change in the rod's magnetization. The direction of current will change according to the frequency of LC circuit which changes direction of magnetic field generated by coil L1.
- This periodic change in direction of magnetic field due to L1 create periodic expansion and contraction in rod with higher frequency.
- This high frequency vibration of rod will generate similar vibrations in surrounding medium which eventually produces ultrasonic waves.
The coil L2 is placed around vibrating rod, an e.m.f. is generated in the coil due to the converse magnetostriction effect. This e.m.f. is then sent back to the base of the transistor. This feedback mechanism helps to maintain the current flowing through the transistor and sustain the vibrations of the rod.
Theory
The frequency of magnetostriction oscillator is given by,
$$\nu = \frac{n}{2l}\sqrt{\frac{Y}{\rho}} $$where Y is the young's modulus of material and \( \rho \) is the density.
Where fundamental frequency is given as,
$$\nu_{fundamental} = \frac{1}{2l}\sqrt{\frac{Y}{\rho}} $$Piezoelectric-Effect
The piezoelectric effect is the ability of certain materials, such as crystals, ceramics, and some plastics, to generate an emf in response to applied mechanical stress. Conversely, when an electric field or voltage is applied to these materials, they can change shape or deform which is called inverse piezoelectric-effect.
Piezoelectric Oscillator
A piezoelectric oscillator is a device that uses the inverse piezoelectric effect to generate ultrasonic waves. It consists of a piezoelectric crystal, typically made of quartz, that is placed under a mechanical stress. When an alternating voltage is applied to the crystal, it periodically changes shape due to the piezoelectric effect or it will start to vibrate ( continous expansion and contraction). This vibration of crystal create vibrations in surrounding medium & generates ultrasonic waves.
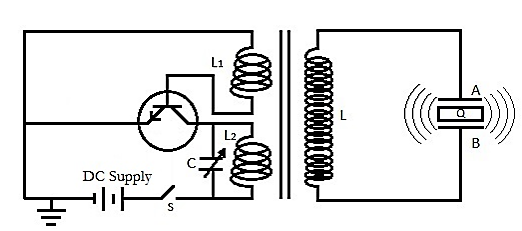
Construction
- A piezoelectric crystal, such as quartz, is used in the construction of a piezoelectric oscillator.
- The crystal is cut in a specific way to produce the desired resonant frequency.
- Electrodes are attached to the crystal's surfaces to apply an electric field and detect the resulting mechanical vibrations.
- An oscillator circuit, such as a LC or tank circuit is connected to the electrodes to generate and sustain the oscillations.
Working
When an electric field is applied to a piezoelectric crystal, it experiences a change in shape due to the inverse piezoelectric effect. This change in shape causes the crystal to vibrate at a certain frequency, known as the resonant frequency.
- When the battery is turned on, the transistor produces current. This current will produce electrical oscillations in LC circuit or tank circuit. This current is then passed through the coil L2, which causes a corresponding change in the magnetic field assosiated with coil L.
- This change in magnetic field induces an emf in circuit ( faraday's law ) and this emf will change the shape of crystal Q. The direction of current will change according to the frequency of LC circuit which changes direction of magnetic field generated by coil L.
- Thus the oscillator circuit applies a varying electric field to the crystal, causing it to vibrate at its resonant frequency. This vibrations in crystal produces vibration in surrounding medium and results in production of ultrasonic wave.
- The coil L1 is placed parallel to inductor L, an e.m.f. is generated in the coil due to the change in magnetic field around inductor L (Mutual induction.). This e.m.f. is then sent back to the base of the transistor. This feedback mechanism helps to maintain the current flowing through the transistor and sustain the vibrations of the crystal.
Theory
The frequency of piezoelectric oscillator is given by,
$$\nu = \frac{n}{2l}\sqrt{\frac{Y}{\rho}} $$where Y is the young's modulus of crystal and \( \rho \) is the density.
Where fundamental frequency is given as,
$$\nu_{fundamental} = \frac{1}{2l}\sqrt{\frac{Y}{\rho}} $$Ultrasonic Diffractometer
When ultrasonic waves are sent through a liquid, the pressure variations cause the density of the liquid to change in alternating layers, creating an "acoustic grating." When a single-color light source is passed through this grating, the light is diffracted. By analyzing this diffraction pattern, the speed of the ultrasonic waves can be calculated.
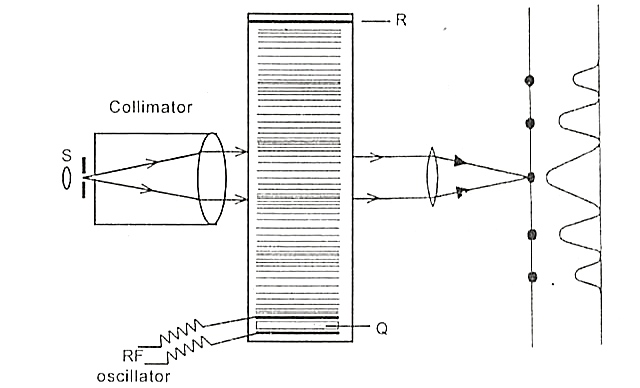
The ultrasonic waves travelling from the RF oscillator get reflected by the reflector placed at the opposite wall. The reflected waves get superimposed with the incident waves producing longitudinal standing wave pattern called acoustic grating. If a monochromatic light is passed through the liquid in a direction perpendicular to the grating, diffraction takes place and we can observe the diffraction pattern on the screen.
Grating equation is given by,
$$ d\;sin\;\theta = n\;\lambda $$where \( \theta \) is angle of diffraction, \(\lambda \) is the wavelength of light used and d is the distance between adjacent node and antinode in accoustic grating.
By finding value of "d", one can calculate wavelength ( because the length 'd' is the half wavelength of ultrasonic wave ) of ultrasonic wave as , $$ v_{ultrasonic} = 2 d $$Detection of Ultrasonic Waves
Ultrasonic waves can be detected through various methods, including thermal detection and piezoelectric detection.
Thermal Detection Method
The thermal detection method uses a temperature change in a material caused by the absorption of ultrasonic waves to detect the presence of ultrasonic waves. This can be done by measuring the temperature change with a thermocouple or thermistor.
Piezoelectric Method
The piezoelectric method uses the piezoelectric effect to detect the presence of ultrasonic waves. A piezoelectric material, such as quartz, is used to detect the ultrasonic waves. When the ultrasonic waves pass through the piezoelectric material, it produces an electrical voltage, which can be measured to detect the presence of ultrasonic waves.
Applications of Ultrasonics
Ultrasonics have a wide range of applications in various fields, including industrial, medical, and scientific research. Some of the most common applications include Non-Destructive Testing (NDT), SONAR, and others.
Non-Destructive Testing (NDT)
Non-Destructive Testing (NDT) is the process of inspecting, testing, or evaluating materials, components or assemblies for discontinuities, or differences in characteristics without destroying the serviceability of the part or system. Ultrasonics are widely used in NDT to detect internal defects in materials, such as cracks, voids, and inclusions.
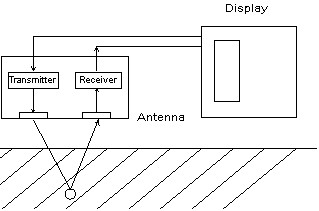
This can be done by sending ultrasonic waves through the material and measuring the diffraction of the waves as they interact with the internal microstructure of the material.
Working
- The ultrasonic waves used in NDT are typically high-frequency (typically in the range of 0.1 to 20 MHz) and are generated by a transducer that converts electrical energy into mechanical energy (sound waves).
- The transducer is typically placed on the surface of the material being tested and sends the ultrasonic waves into the material.
- The waves travel through the material and, as they encounter internal defects, they are reflected, refracted, or diffracted back to the surface.
- The transducer then receives the waves that have returned to the surface and converts them back into an electrical signal.
- The electrical signal is then analyzed by specialized equipment, such as a pulse-echo or through-transmission system, to determine the location, size, and type of any defects present in the material.
SONAR
SONAR (Sound Navigation and Ranging) is a technology that uses ultrasonic waves to detect and locate objects under water. The SONAR system works by emitting an ultrasonic pulse and measuring the time it takes for the pulse to be reflected back from an object.
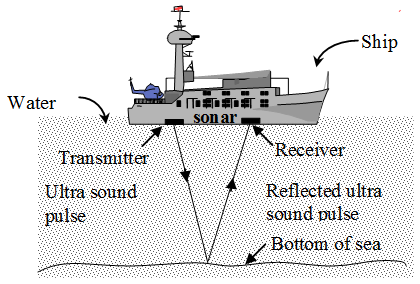
- A sonar system typically consists of a transmitter (or transducer) that generates and sends out a sound wave, and a receiver that listens for the returning echoes of the wave.
- The transmitter generates a short burst of sound, usually in the form of a pulse, and sends it into the water.
- The sound wave travels through the water, and when it touches bottom of sea, some of the energy is reflected back to the surface as an echo.
- The receiver, which is located near the transmitter, listens for the returning echoes and measures the time it takes for the sound to travel to the object and back.
- By measuring the time delay between the transmitted pulse and the received echo, the sonar system can calculate the depth of sea.
Other Applications
Ultrasonics have a wide range of other applications, including:
- Cleaning - Ultrasonic cleaning is a method of cleaning that uses ultrasonic waves to agitate a cleaning solution, resulting in a more thorough cleaning of the object being cleaned.
- Welding - Ultrasonic welding is a method of welding that uses ultrasonic waves to heat and weld two pieces of material together.
- Medical - Ultrasonics are used in medical imaging, such as ultrasound and Doppler imaging, to create images of internal organs and blood vessels.
- Industrial - Ultrasonics are used in industrial applications such as measuring the level of liquids in tanks and the thickness of materials in manufacturing.
Numerical problems
- Calculate the fundamental frequency of vibration of quartz crystal of thickness 12mm at
resonance
if its Young`s modulus is \( Y=7.5 X 10^{10} N/m^2 \) and density, \(\rho= 2500 kg/m^3 \)
Answer:
We know the expression for fundamental frquency of piezo-electric oscillator as,
$$\nu_{fundamental} = \frac{1}{2l}\sqrt{\frac{Y}{\rho}} $$Where Y is the youngs modulus of material and \( \rho \) is the density.
Given quantities are ;
$$ Thickness,\;l=12 \;mm = 12 \times 10^{-3}\;m $$ $$Young's\;modulus,\;Y=7.5 \times 10^{10} N/m^2 $$ $$Density,\;\rho=2500\;kg/m^3 $$
Substituting this given quantities in equation of fundamental frequency,
$$\nu_{fundamental} = \frac{1}{2l}\sqrt{\frac{Y}{\rho}} $$ $$\;\; = \frac{1}{2\times 12 \times 10^{-3}}\sqrt{\frac{7.5 \times 10^{10}}{2500}} = 228217.73\;Hz$$So the crystal have a fundamendal frequency of 228217.73 Hz
- Calculate the fundamental frequency of vibration of ferromagnetic rod of thickness 5mm at
resonance
if its Young`s modulus is \( Y=8 X 10^{10} N/m^2 \) and density, \(\rho= 2650 kg/m^3 \)
Answer:
We know the expression for fundamental frquency of magnetostriction oscillator as,
$$\nu_{fundamental} = \frac{1}{2l}\sqrt{\frac{Y}{\rho}} $$Where Y is the youngs modulus of rod and \( \rho \) is the density.
Given quantities are ;
$$ Length,\;l=5 \;mm = 5 \times 10^{-3}\;m $$ $$Young's\;modulus,\;Y=8 \times 10^{10} N/m^2 $$ $$Density,\;\rho=2650\;kg/m^3 $$
Substituting this given quantities in equation of fundamental frequency,
$$\nu_{fundamental} = \frac{1}{2l}\sqrt{\frac{Y}{\rho}} $$ $$\;\; = \frac{1}{2\times 5 \times 10^{-3}}\sqrt{\frac{8 \times 10^{10}}{2650}} = 549442.25\;Hz$$So the ferromagnetic rod have a fundamendal frequency of 549442.25 Hz